Esse tema ganhou relevância na indústria de máquinas e, processos do Brasil nos últimos 14 anos, especialmente depois das privatizações de grandes empresas geradoras de eletricidade no governo FHC e, das demandas mais recentes do Pré-Sal. Atualmente, já não é tão difícil se deparar com controladores digitais com a capacidade de registro de eventos (SOE), principalmente eventos discretos (lidos a partir de ED´s).
O problema é que as máquinas e, processos industriais são constituídos de eventos digitais, mas também analógicos (lidos a partir de EA´s). Os eventos podem ser Alarmes e, também os famosos TRIP´s e Shutt-Down´s, oriundos de ocorrências físicas discretas ou analógicas.
Hoje, poucos controladores tem a capacidade de registrar eventos analógicos da maneira correta e, nem todos os controladores que dizem oferecer a opção de registro de eventos analógicos o fazem na prática. Esse artigo tem o propósito de esclarecer aos usuários desse tipo de recurso como funciona de fato o registro de eventos analógicos (ou SOE analógico), sua importância e, benefícios, pois têm ocorrido alguns erros de interpretação no mercado quanto essa forma importante de monitoramento, seja do lado do usuário, seja do lado de alguns fornecedores de controladores digitais.
Esse artigo focará especialmente o registro de eventos em sistemas auxiliares de turbo-máquinas (turbo-geradores e turbo-compressores), embora sua aplicação seja mais abrangente.
Introdução
Apenas para recordar, registro de evento, também conhecido popularmente como SOE (Sequence Of Events), nada mais é como a capacidade de um controlador digital gravar uma estampa de tempo quando ocorre uma variação em suas entradas (discretas ou analógicas).
O objetivo deste recurso é, por exemplo, permitir ao usuário mapear com mais facilidade uma cadeia sequencial de eventos causadora de algum distúrbio ocorrido em planta industrial, seja numa máquina ou processo, permitindo um diagnóstico e manutenção mais rápida da causa desse distúrbio, de maneira precisa e, confiável.
As primeiras experiências com registro de eventos no âmbito industrial ocorreram na década de 80 em refinarias de petróleo da região de Houston, no estado do Texas-EUA, em turbinas à vapor e gás que acionavam trens de compressores. Os controladores empregados na ocasião tinham a capacidade de monitorar, ainda que limitadamente no que diz respeito a quantidade eventos/scan, ocorrências digitais e, analógicas.
Depois houve uma grande expansão do emprego desse recurso na área de geração energia também (usinas térmicas e hidrelétricas). Uma confusão que ocorre hoje no mercado em alguns momentos é comparar registro de eventos com oscilografia, especialmente para registro de evento analógico. Uma coisa não tem relação direta com a outra, embora algumas características da oscilografia possam ser observadas no registro de eventos analógico também e, vice-versa.
Os controladores que fazem uso do recurso de registro de eventos podem usar seu próprio relógio (Clock) para disponibilizar a estampa de tempo necessária (geralmente no formato ANO-MÊS-DIA-HORA-MINUTO-SEGUNDO-MILISSEGUNDO) ou empregar uma base de tempo universal, através do uso de GPS, utilizando para sincronização do relógio do controlador pulsos carregados através dos protocolos de tempo mais comuns de mercado, tais como o SNTP (IEC 61850), IRIG-B, CIP Sync (IEEE 1588), entre outros. Tradicionalmente e, tecnicamente falando, fixa-se a precisão para eventos digitais em 1 ms ou 2 ms (mais comum 1 ms) e, analógicos em 5 ms. Os eventos digitais são estampados tanto na subida (1) quanto na descida (0).
Já os analógicos são estampados na falha ou na variação (ver figuras 4 e 5) e, é o que deve ser considerado basicamente, nada mais que isso. Entretanto, para uma análise confiável de eventos analógicos, às vezes é necessário se avaliar uma sequência temporal de uma ou mais grandezas, dentro de vários intervalos de 5 ms, para se chegar a um diagnóstico preciso.
Essa análise muitas vezes é comparada em paralelo com o histórico de eventos digitais (de 1 ms) também, para se identificar quem iniciou o distúrbio, se foi um SOE digital ou SOE analógico, quando o processo assim requerer.
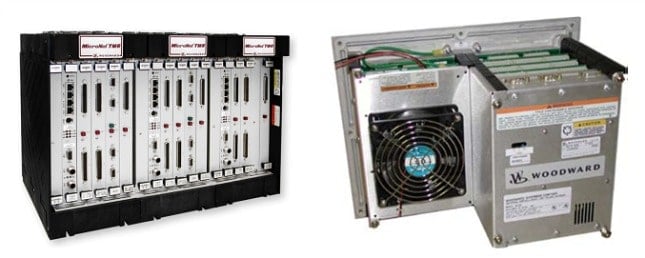
Requisitos Mínimos do Controlador Digital para Suportar Registro de Eventos Digitais e Analógicos
Boa parte dos controladores digitais de mercado tidos como de “médio ou grande porte”, já incorporam a capacidade de registro de eventos digitais. No entanto, para que o mesmo controlador também possa ter a capacidade de incorporar registro de eventos analógicos de maneira adequada, é recomendável ele ter pelo menos 2 características importantes de hardware e software, por se tratar de grandeza “variante no tempo”: Determinismo e Recursividade (ver figura 2).
São poucos os controladores que incorporam estas 2 características no mercado, já que existe a necessidade da “sincronização” de todas as E/S paralelamente ao Scan do Controlador . Para registro de eventos digitais, o Determinismo e Recursividade não são tão importantes, por se tratar de grandeza “invariante no tempo”. Os bons controladores devem ter capacidade para registrar entre 50 e 200 eventos (digitais e analógicos) a cada Scan.

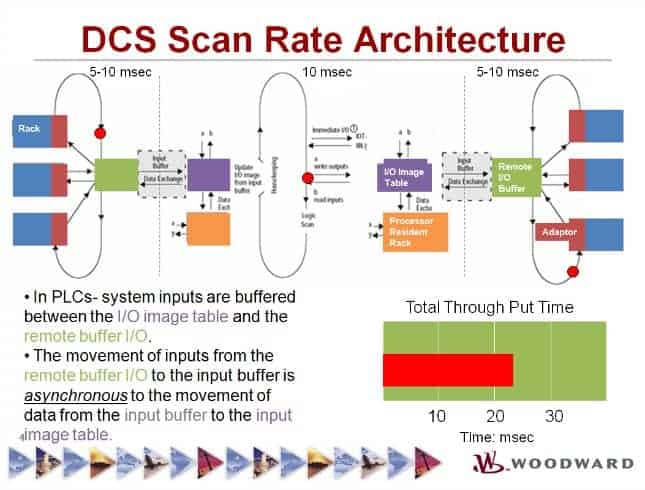
Exemplo de Aplicação em Turbo-Compressor
Primeiramente se atendo aos eventos analógicos apenas, turbo-compressores são considerados uma das aplicações mais críticas dentro da indústria de Óleo & Gás, pois estas máquinas são responsáveis por trabalhar toda a sorte de gases essenciais ao processo industrial, sejam gases refrigerantes, combustíveis, de efeito químico e outros. Os (bons) controladores instalados em turbo-compressores devem ser capazes de prever com antecedência a ocorrência de distúrbios que precedem um evento chamado SURGE.
Esse SURGE é um evento característico de compressores. Ele é danoso e, deve ser evitado a todo custo, devido sua altíssima criticidade sobre a máquina e processo. Um turbo-compressor de porte médio ou grande possui diversos sensores de pressão e fluxo, e justamente o monitoramento destas grandezas em tempo real é que pode possibilitar uma ação prévia que permita o acionamento da proteção ANTI-SURGE em tempo adequado.
Ocorre que num turbo-compressor médio ou grande, as variações de fluxo e pressão podem ocorrer quase que simultaneamente nos diversos canais sensoriados. Uma vez acionada a proteção ANTI-SURGE, entra em cena o registro de eventos analógicos, para que a equipe de manutenção e análise possa diagnosticar qual dos canais sensoriados iniciou o distúrbio e, fazer as devidas correções de maneira precisa.
Veja abaixo um gráfico ilustrativo para melhor compreensão:
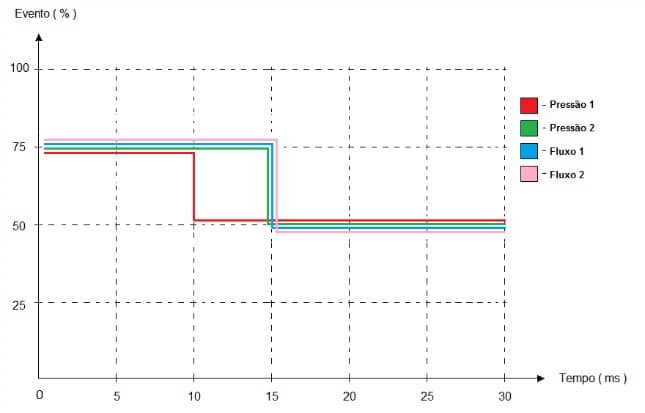
Nota Importante: No exemplo da figura 4 (e outras figuras adiante), os eventos ocorrem de maneira linear/proporcional e, em intervalos temporais fixados a partir de 5 ms somente para facilitar a interpretação de caso neste artigo técnico, mas na prática, ocorrem variações distintas do t=0 de cada grandeza envolvida, sem falar da não-linearidade/proporcionalidade de evento.
Fica claro neste exemplo que os distúrbios no turbo-compressor iniciaram por uma variação na Pressão 1, que acabou “arrastando” as demais grandezas monitoradas. Portanto, fica fácil, através do registro de eventos analógicos, identificar que iniciou o distúrbio, facilitando o trabalho de manutenção e, correção. Vale recordar, como dito no inicio deste artigo, que o registro de evento analógico atua na falha ou variação. Vejamos abaixo um exemplo agora, para o mesmo caso, supondo uma falha da entrada analógica, por razão de um cabo hipoteticamente rompido. Dependendo do fabricante do controlador, o valor monitorado poderá ir para fundo de escala ou para zero.
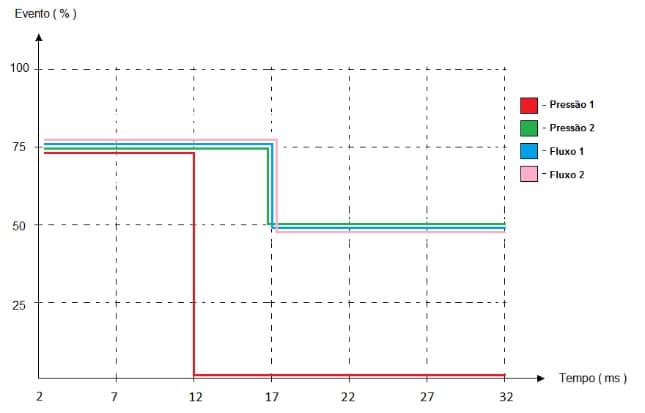
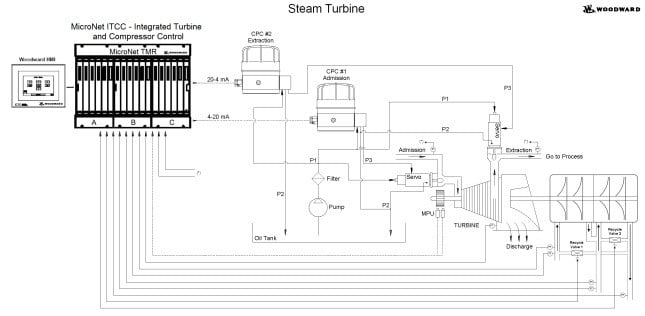
Exemplo de Aplicação em Turbo-Gerador (Hidrelétrica e Termelétrica)
Agora, veremos um exemplo de aplicação em usinas hidrelétricas e, térmicas, combinando o monitoramento de grandeza analógica com digital. No Brasil esta se tornando comum o emprego de registro de eventos em usinas maiores que 30 Mw (UHE´s ou UTE´s), porém somente o monitoramento de eventos digitais na grande maioria e, poucos casos de monitoramento de registro de evento analógico. Numa usina hidrelétrica ou térmica, existe uma infinidade de eventos digitais e, analógicos capazes de provocar um TRIP do turbo-gerador.
Como exemplo citamos a abertura indevida de um disjuntor (digital) e uma sobre-temperatura do óleo de lubrificação do mancal de escora da turbina (analógico), causando o TRIP.
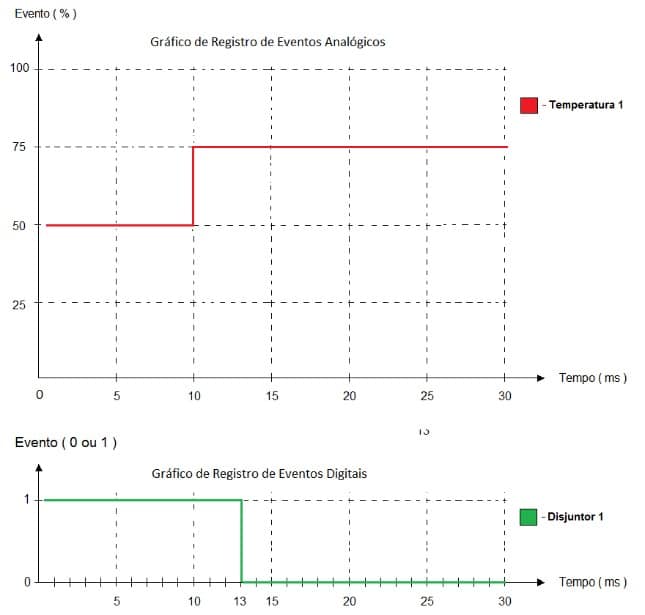
Neste exemplo da figura 7 ficou evidente que uma sobre-temperatura no instante t=10 ms provocou um TRIP da turbina e, que posteriormente desencadeou uma sequência de eventos de proteção da lógica funcional da máquina.
Observe neste exemplo que 3 ms após a ocorrência da sobre-temperatura de TRIP, no instante t=13 ms, ocorreu a abertura de um disjuntor, que fazia parte da lógica de intertravamento funcional de proteção do sistema.
Caso não houvesse o monitoramento do evento analógico (sobre-temperatura), o diagnóstico sobre a ocorrência inicial causadora do TRIP ficaria concentrado somente sobre o evento digital (abertura do disjuntor), gerando uma conclusão imprecisa sobre a causa original do fato e, por seguinte, uma intervenção improdutiva da equipe de manutenção para as correções, com perdas de tempo e, gastos desnecessários.
Instalações Existentes
Instalações existentes que monitorem somente eventos físicos digitais não demandam qualquer intervenção. No entanto, existem diversos casos de instalações que eventos físicos analógicos são “convertidos” para uma condição digital.
Um exemplo típico é utilizar um sensor de pressão, que possua além da sua respectiva saída analógica, uma saída auxiliar (de alarme) em contato seco. Esse tipo de conversão pode introduzir um atraso de alguns milissegundos no sistema, gerando um relatório temporal de eventos impreciso.
Isso pode ser aferido levando a saída analógica e saída digital do mesmo sensor para o controlador digital, realizar o teste SOE da sobre-pressão e, comparar os registros de eventos analógico e, digital em paralelo. Não existe uma regra, mas em tese podemos considerar que, se o SOE analógico ocorrer antes do SOE digital no respectivo ensaio, numa diferença superior a 2 ms, é recomendável a instalação passar por uma re-adequação (re-engenharia).
Se a diferença for inferior a 2 ms, fica a critério do usuário partir para uma re-adequação da instalação. Se os tempos forem iguais em pelo menos 3 ensaios, não haverá necessidade de qualquer re-adequação.
Uma forma de re-adequação, digamos econômica, considerando diversos ensaios em pontos diferentes, seria a introdução de somadores ou subtratores no relógio de software do controlador, para suprimir as diferenças temporais.
Por fim, o ideal, seria a substituição do controlador por um modelo que suporte SOE digital e SOE analógico e, uma re-engenharia de maior porte.
Cuidado com os Protocolos de Tempo
Atualmente, os protocolos de tempo mais utilizados em projetos de automação de turbinas no Brasil são o IRIG-B e, o SNTP.
O protocolo IRIG-B é bastante preciso, opera em rede padrão Serial dedicada e, é usado por fabricantes tradicionais de equipamentos tais como Siemens, General Electric, SEL, entre outros. Já o protocolo SNTP, também bastante preciso, mas diferentemente do IRIG-B, é um protocolo mais recente, opera em rede Ethernet de propósito geral e, é utilizado por fabricantes tradicionais tais como ABB, Woodward, Schneider Electric, Altus, entre outros.
Outro ponto importante a frisar é que o SNTP é o padrão adotado pela norma IEC 61850 (norma tradicional que trata de comunicação entre IED´s muito usados em subestações de energia e, sistemas de potência).
Embora ambos protocolos sejam muito bons e, atendam plenamente as necessidades dos usuários, um cuidado muito importante deve ser tomado, quanto a compatibilização de ambos protocolos, quando os mesmo são empregados numa mesma planta ou plantas separadas interligadas por linhas de transmissão.
Para melhor entendimento do caso, vamos ilustrar a situação em 2 exemplos:
Exemplo 1:
Uma mesma usina, utilizando um equipamento sincronizado por IRIG-B e, outro equipamento sincronizado por SNTP.
Neste caso, um mesmo GPS com saídas IRIG-B e SNTP envia simultaneamente o pulso de sincronismo para um Controlador A que opera em IRIG-B e, para o Controlador B que opera em SNTP.
A estampa de tempo enviada para ambos controladores pelo GPS é exatamente a mesma. Em tese, poderíamos supor que os 2 controladores terão exatamente a mesma estampa de tempo sincronizada, mas na prática isso não ocorre. O motivo é que o pulso de sincronismo oriundo do GPS chega com alguns milissegundos de atraso no Controlador A, se comparado com o Controlador B.
Isso ocorre por diversos fatores, mas em especial porque o Controlador A, operando em IRIG-B, usa uma rede Serial para transportar o pulso de sincronismo e, a velocidade de tráfego de comunicação desta rede é muito inferior a rede Ethernet, empregada no Controlador B, que opera em SNTP (ver Figura 8).
Num projeto de automação de uma hidrelétrica da Chesf (Cia Hidrelétrica do São Francisco), foi usado um GPS nacional, com saídas IRIG-B e SNTP, um CLP nacional e, um Regulador de Velocidade ( RV ) de turbinas norte-americano. O CLP recebia o pulso de sincronismo em IRIG-B e, o RV em SNTP. Foi constatado, após vários ensaios, que a defasagem de tempo entre ambos equipamentos ficou na casa de 160 ms.
A solução no caso era inserir um somador de tempo no CLP ou um subtrator de tempo no RV. Foi decidido de comum acordo, neste projeto em especifico, usar um subtrator de tempo no RV, o que resolveu o problema.
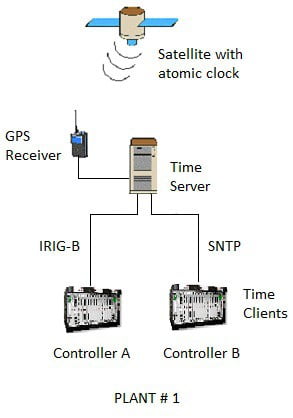
Exemplo 2:
Duas usinas (1 e 2) distantes 900 Km uma da outra, no entanto interligadas por uma linha de transmissão em alta tensão, sendo que a usina 1 utiliza equipamentos sincronizados por IRIG-B e, a usina 2 utiliza equipamentos sincronizados por SNTP.
Neste caso, os equipamentos da usina 1 são sincronizados por um GPS local em IRIG-B e, os equipamentos da usina 2, sincronizados pelo GPS local em SNTP. Ambas usinas estão interligadas eletricamente por uma linha de transmissão de 500 KV, na distância de 900 Km (ver Figura 9).
Cada usina é operada por um concessionário distinto. Em determinado momento, ocorre uma perturbação no sistema, desarmando a linha de transmissão e, as usinas 1 e 2, tudo simultaneamente.
A origem de causa da perturbação passa a ser investigada em ambas usinas através dos relatórios de eventos respectivos, para tomada das correções necessárias, apuração de responsabilidades e, eventual cobrança de indenizações contra o concessionário causador do distúrbio, por razão da parada de produção.
Embora ambas usinas utilizem controladores digitais, sincronizados por GPS, o que em tese, tornaria fácil a comparação dos relatórios eventos para determinação da causa origem da perturbação, o fato dos equipamentos serem sincronizados por protocolos de tempo distintos poderá gerar relatórios e, uma conclusão imprecisa sobre a causa fonte do distúrbio, se não for considerada a defasagem temporal entre o IRIG-B e SNTP.
Para que a análise seja precisa, será preciso imputar no relatório de alguma usina o “delay” necessário para equalizar os tempos, para fins de comparação.
Esse delay pode inclusive ser adicionado ao relatório automaticamente, através de algum botão do Scadda local, com script especifico ou direto no controlador, mais confiável (ver Figura 10).
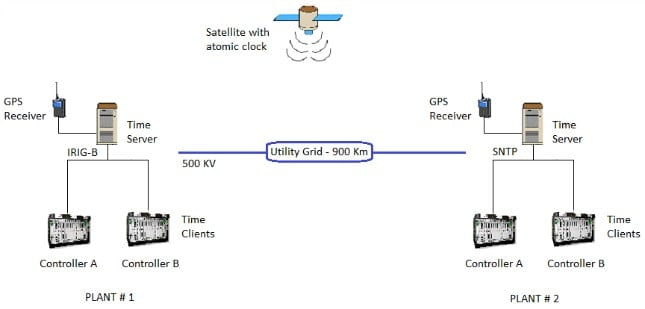
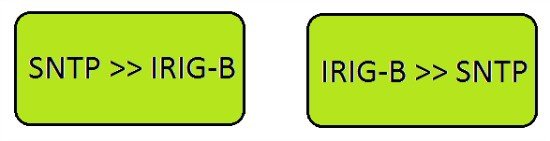
SNTP
Por fim, existe uma tendência cada vez maior para o uso do SNTP em aplicações de registros de eventos físicos digitais ou analógicos. A razão é sua boa precisão, compatível com as necessidades dos usuários, a facilidade da implementação deste protocolo nos equipamentos industriais, o uso da rede Ethernet e, sua padronização pela norma IEC 61850.
Um Inconveniente do Registro de Eventos Analógicos
A implantação do registro de eventos analógicos é muito importante nos projetos de automação, mas deve ser realizada com muito critério e, cautela.
A razão é que, por se trabalhar com grandeza “variante no tempo”, isso demanda um grande consumo de memória e, espaço de tráfego de comunicação nos sistemas de automação (controladores, redes, supervisórios, etc), mesmo comunicação por exceção, muito superior aos sistemas que monitoram somente registro de eventos digitais, que trabalham com grandezas “invariantes no tempo”.
Alguns controladores permitem inclusive a introdução de 1 ou 2 Set-Points Low e High no SOE analógico, o que pode limitar a banda de monitoração, reduzindo o consumo de memória e, espaço de trafego em rede.
Outro ponto muito importante é que a análise de um relatório de SOE analógico deve ser feita com muito mais cuidado se comparado a análise de um relatório de SOE digital, especialmente se o relatório de SOE analógico estiver sendo comparado com o relatório de SOE digital, como foi exemplificado na figura 7.
Benefícios de uso do SOE Analógico
Abaixo, um resumo dos benefícios do SOE analógico:
- A certeza de ter todas as grandezas do processo realmente monitoradas e, de forma correta;
- Evitar a geração de relatórios imprecisos;
- Evitar o emprego de “conversões” analógicas para digitais, através do uso de contatos secos, que podem introduzir “atrasos” indesejáveis no sistema.
Conclusão
Fica concluído portanto a importância de se monitorar não somente o SOE digital, mas também o SOE analógico.
Somente com o monitoramento desses dois tipos de SOE´s é que o usuário terá a certeza enfim de contar com um relatório que possa lhe trazer a confiabilidade esperada para análise de ocorrências, atacando de maneira precisa o problema da máquina ou processo, gerando redução de custos e, eficácia nas ações de manutenção.
Referências Bibliográficas
- Analog Time Stamping – Doc 26166v1 – Revision D – Woodward Governor Company
- RFC 2030 SNTP – Version 4 Publication
4 Comentários
Olá meu caro muito bom artigo, e é bom saber que você faz parte da equipe da Woodward.
Estou num projeto em Sta Vitória onde o controle de velocidade, sincronismo e proteção de sobrevelocidade são Woodward.
Em breve precisarei da ajuda de vocês para treinamentos da equipe e definição de um estoque estratégico destes sistemas.
Um abraço.
Paulo.santos@steag.com.br
Legal Paulo, muito grato por apreciar o artigo, a disposição… Um abraço, Ronaldo – ronaldo-jsilva@bol.com.br
Muito bom o artigo!
Gostaria de saber na sua opinião qual será o impacto da indústria 4.0 para usinas Hidroelétricas (UHE) ?
Abraços,
lucas.pllopes@gmail.com
Boa noite Lucas ! Muito grato por apreciar o artigo. Vou responder sua pergunta em 2 partes.
1º As UHE´s no Brasil vem se modernizando de maneira robusta nos últimos anos, sejam usinas novas ou retrofits. Particularmente, considero um dos setores onde é possível implementar de maneira mais eficiente a automação ( pela norma IEC 61131 uma UHE é considerada “processo” ), já que desde a segunda metade da década de 90 ( 96 p/ frente ) já existiam usinas tele-comandadas, eu mesmo participei do primeiro projeto do tipo no Brasil, na PCH Eloy Chaves da CPFL ( um espetáculo de projeto para a época ). Com a chegada da Industria 4.0, que basicamente promove a Integração massiva de TA + TI + Internet das Coisas ( IoT ) + Digitalização Imensa de Dados = Big Data, veremos muito em breve, por exemplo, instrumentação de campo inteligente enviando de maneira autonoma dados para o topo de pirâmide ( Ex. caixa de e-mail de um gestor ), informando por exemplo a hora desse instrumento passar por uma manutenção preventiva ou preditiva ( não apenas corretiva ) para tomada de ações. Parece pouco, mas não é, isso é um impacto significativo, pois a partir do momento que o instrumento de campo toma esse tipo de iniciativa, passamos a reduzir ainda mais a intervenção humana, o que pode ser bom ou ruim, dependendo da forma que isso é administrado, pois isso também é feito hoje de maneira inteligente, só que do lado de cima de certa forma. Então, como o conceito de Industria 4.0 é novo, com certeza o as UHE´s irão passar nos próximos anos por uma intensa atualização dos eqptos, desde no nível de instrumentação, passando pelo nível de controle, chegando no nível planta ( topo da pirâmide ). Particularmente, acho que a Industria 4.0 irá de vez “achatar” a tradicional pirâmide da Automação como conhecemos hoje, acho isso bom !
2º No tocante aos tópicos desse artigo, existe uma relação importante entre eles e, a Industria 4.0. Explico: Hoje, o conceito de SOE Analógico é pouco explorado nas UHE´s de maneira correta, então com a chegada da Industria 4.0, que leva em consideração a digitalização massiva de dados para tomada de decisões ( Big Data = registro dos dados ), o SOE passa se incluir nesse cenário, em especial o Analógico, hoje tão negligenciado, o que é inaceitável no conceito de Big Data e, Internet das Coisas ( IoT ) da Industria 4.0. O SOE Analógico contribui com impacto significativo para um dos grandes objetivos da Industria 4.0 que é a busca incessante pelo aumento da produtividade, com redução de custos e, elevação da qualidade. Tudo isso vai com certeza acontecer nas UHE´s Brasileiras ( e nos outros segmentos da indústria ), talvez não tão rápido como gostaríamos, mas vai acontecer.
Espero ter de alguma forma ter respondido sua questão, ela foi bem ampla, seria objeto de várias formas de resposta, pois o assunto é extenso, mas foi o que me veio na cabeça agora, mas uma coisa eu lhe digo, a Industria 4.0 veio para ficar…
Felicidades e, um abraço, Ronaldo – ronaldo-jsilva@bol.com.br